Radial ball bearings
Radial ball bearings use balls as rolling elements and have a contact angle less equal 45°. Most important types are radial deep groove ball bearings and angular contact ball bearings.
Deep groove ball bearing
Deep groove radial ball bearings are one of the best-known examples of rolling bearing types and are reasonably suitable for a wide range of applications. Moreover, they count with a robust, non-separable and simple design that, together with low maintenance requirements and cost, makes them the most widely used bearing in the market. The geometry of a deep groove ball bearing is described with number and diameter of balls, pitch diameter, conformity of inner and outer race and the diametric clearance. The nominal contact angle is 0°, which is increased under axial load depending on the radial clearance in the bearing. The X and Y coefficients for calculating the equivalent dynamic load are load-dependent as the contact angle varies with the operating load due to resulting deformations. The number of balls in the bearing is restricted in order to be able to assemble the bearing, which can be optionally sealed or shielded. It can fairly support a pure radial load and axial loads in double direction and also acceptably perform the non-locating bearing role. It behaves poorly under moment loads, or when compensating misalignments in operation or induced errors of initial alignment. So all in all, it has excellent capabilities for high operational speeds and high running accuracy, as well as a very quiet running, fair stiffness and very low friction.
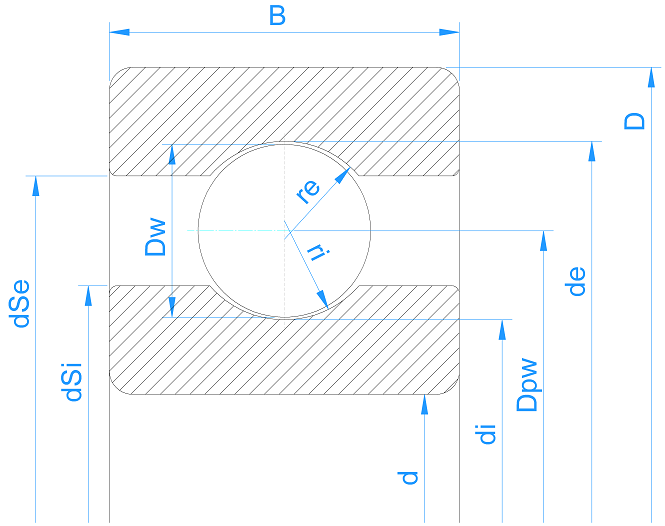
Deep groove radial ball bearing (double row)
Double row deep groove ball bearings are equivalent in design to single row deep groove ball bearings, but the geometry is additionally determined by the distance between rows ‘δR’ and do not have seals nor shields. As they are a little wider than single row bearing for the same bore and outside diameter, they are suitable for bearing arrangements where the load carrying capacity of a single row bearing is inappropriate. Furthermore, they are able to support moment loads satisfactorily. Nevertheless, they have limited levels of stiffness and achieve worse running accuracies and high-speed capabilities than single row ball bearings.
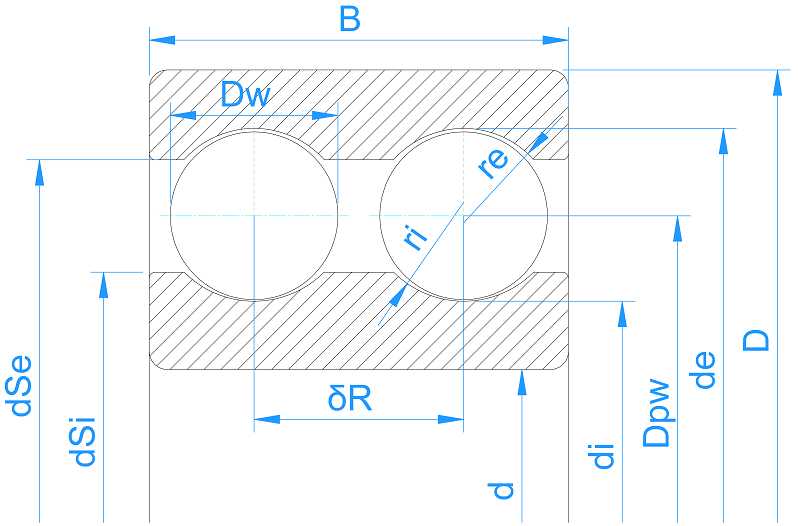
Radial angular contact ball bearing
The angular contact ball bearings are designed to have contact angles larger than 0°, which according to the standards are 15°, 25° or 40°. This is achieved by building the rings symmetrically displaced to each other in the direction of the bearing axis and having one high and one low shoulder. The idea is to get larger axial load carrying capacities as the contact angle increases. The contact angle is contained in the bearing’s cross section plane and defined between the line joining the contact points and a line perpendicular to the bearing axis. In this way, a single row bearing is considerably good accommodating radial and axial load at the same time, but the axial loads are supported in one direction only; pure axial or radial loads are fairly supported. The single row angular contact ball bearings are typically mounted against a second bearing in order to form a set that results in the so-called O, X or Tandem configurations. Moment loads or compensation of misalignments are very poorly achieved and the non-locating role cannot be performed. High running accuracies are possible with good high-speed capabilities and quiet running. They offer an intermediate level of stiffness and their level of friction is low, although higher than the one for deep groove ball bearings.

Radial angular contact ball bearing (double row)
They are equivalent in design to two single row angular contact ball bearings arranged in O-configuration, but result in narrower widths. They can be shielded or sealed and are non-separable, unless they are built with a split inner ring. They are better in supporting radial loads and the axial loads can be accommodated in both directions. Unlike single row angular ball bearings, moment loads can be fairly withstood, offer a higher stiffness and the non-locating role can be performed. However, their running is not as quiet as in the case of single row sets and they undergone worse friction conditions. They deliver a lower running accuracy and the compensation for misalignments or alignments errors is not possible.
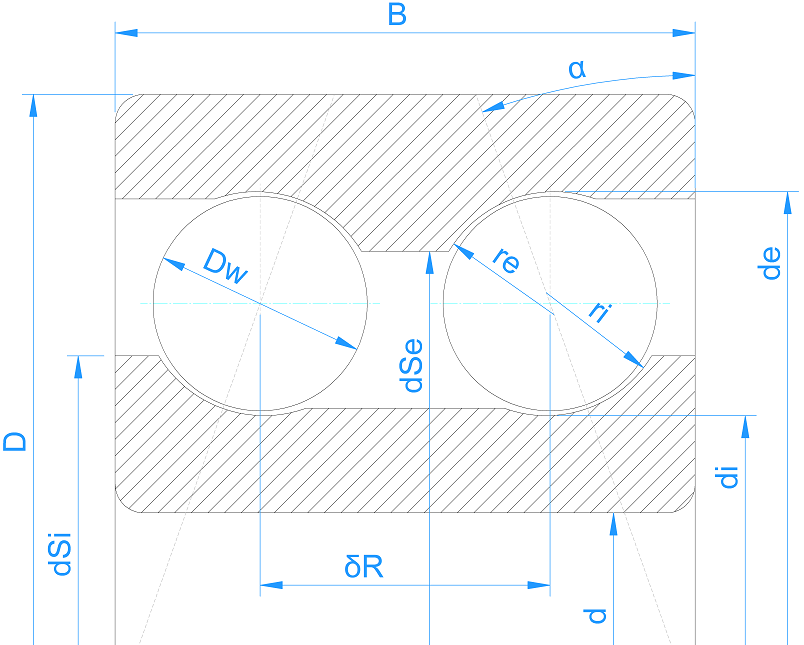
Self aligning ball bearing (Double row)
Self-aligning ball bearings consist of two rows of balls running separately on a two-raceway inner ring, but held in a common sphered raceway built in the outer ring. This design reduces the frictions more than any other type of rolling bearing, so very high speeds and at running accuracy can be reached. They remain unaffected under relative angular misalignment between the shaft and the housing and therefore can optimally compensate alignment errors. As the angle of the bearing can be modified, they are unsuitable to support moment loads. It could be fairly used as non-locating bearing or to take pure radial loads, however behaves poorly under pure axial load and deliver a very low stiffness. They can be normally found in open or sealed versions with a cylindrical or tapered bore, but cannot be disassembled.
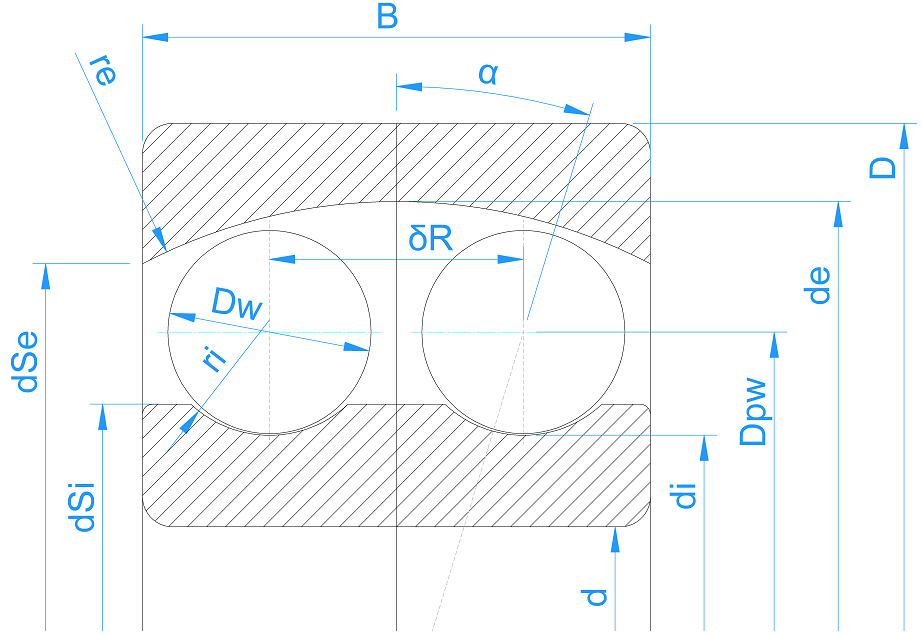
Self aligning ball bearing
They have an equivalent working principle to the double row self-aligning ball bearings but with reduced load capacities in comparison. Nevertheless, they might accommodate higher tilting angles resulting from shaft misalignments.
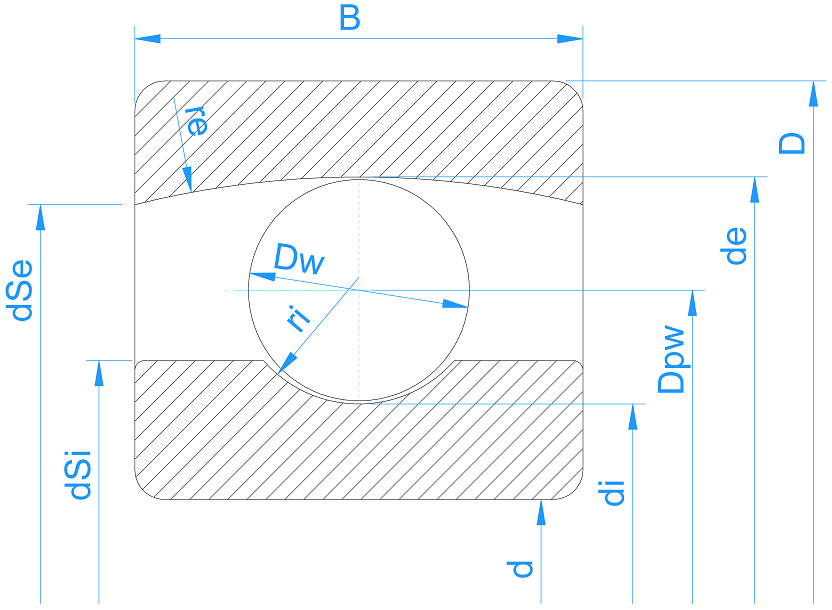
Four point ball bearing
The four-point contact ball bearings are radial single row angular contact ball bearings whose raceways have been ideally devised to carry either pure axial loading in both directions or combined loading provided that the axial component is more significant. Nevertheless, pure radial loads are accommodated quite badly. This bearings are separable, as they consist of a two-piece inner ring that allows a large number of balls to be introduced, thus increasing the load carrying capacity. The capacity to undergone moment loads is good and their stiffness level is comparable to deep groove and angular contact ball bearings. They can be subjected to high speeds, however the four-point bearings does not offer a good performance in terms of running accuracy, friction and quiet operation. They are unsuitable to compensate misalignments, and its use as non-locating bearing is not recommended but possible.
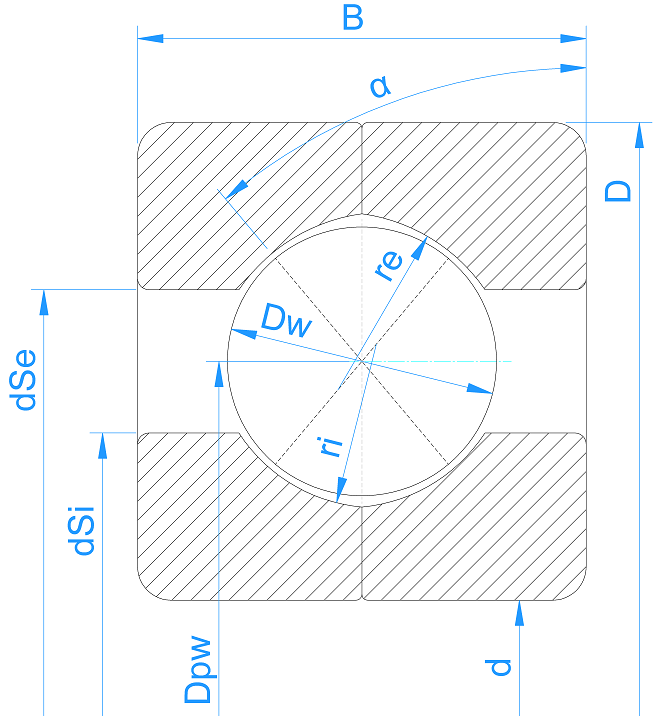
Duplex bearings
Duplex bearings are normally two matched deep groove radial ball bearings. The inner and/or outer ring faces are selectively relieved by a precise amount known as the preload offset. During mounting on the shaft, the desired preload is achieved by driving the inner and/or outer rings of the bearings towards each other until the offset in between is removed. This method of preload can be the simplest for the user, as it offers the advantage of a built-in preload instead of using springs. Duplex bearings have a higher load capacity compared to a single bearing and can withstand bi-directional thrust loads. They deliver accurate bearing positioning in radial and axial directions from a defined clearance to controlled radial and axial rigidity. Their speed capability is normally limited as a result of the heat generated by the rigid preload. Usually, the matches of deep groove radial bearings have a preload of 5 N and a nominal contact angle of 10°-15°, therefore the lines that pass through the contact point of the rolling elements (load lines) tend to converge outside the bearing, as it happens in a O-configuration of an angular contact ball bearing set. In only a few applications, X-configuration could be also used, where a misalignment must be accommodated but having a lower speed capability. A Tandem configuration could be used to counter heavy thrust loads in only one direction, however a spring preloading would have to be installed.
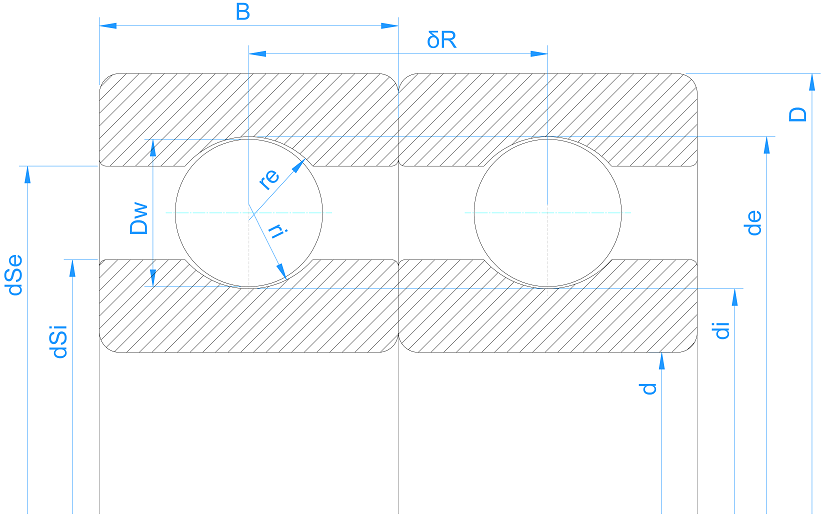