Radial roller bearings
Radial roller bearing use either cylindrical, tapered or spherical rollers and have a contatc angle less equal 45°. Most important types are radial cylindrical roller bearings, taper roller bearings and double row spherical roller bearings.
Cylindrical roller bearing
Cylindrical roller bearings can mainly be differentiated in single and double row, with and without cage (full complement). The basic design of consists of two integral flanges, whose inward face is inclined by a certain angle, on either the inner or outer ring to guide the rollers. In this way, they are particularly appropriate for the non-locating role, as axial displacements are possible. A common modification of this basic design is to add flanges on both rings, and through the resulting possible configurations, the bearings are enabled to handle pure axial loads in either direction or general combined load cases. This gives rise to the known variants like NU, N, NJ…
Single row bearings with a cage can put up with heavy radial loads, fast accelerations and high speeds. The rollers have a logarithmic profile. By using a logarithmic profile, the misalignment and shaft deflection is reduced and the loads are evenly distributed along the rollers, what prevents stress peaks at the roller ends, thus extending the bearing service life.
Full complement bearings are aimed to incorporate the maximum number of rollers and are thereby suitable for very heavy pure radial loads at moderate speeds. They have an excellent behavior in applications where high stiffness is required, however they operate more noisily and have more frictional loses.
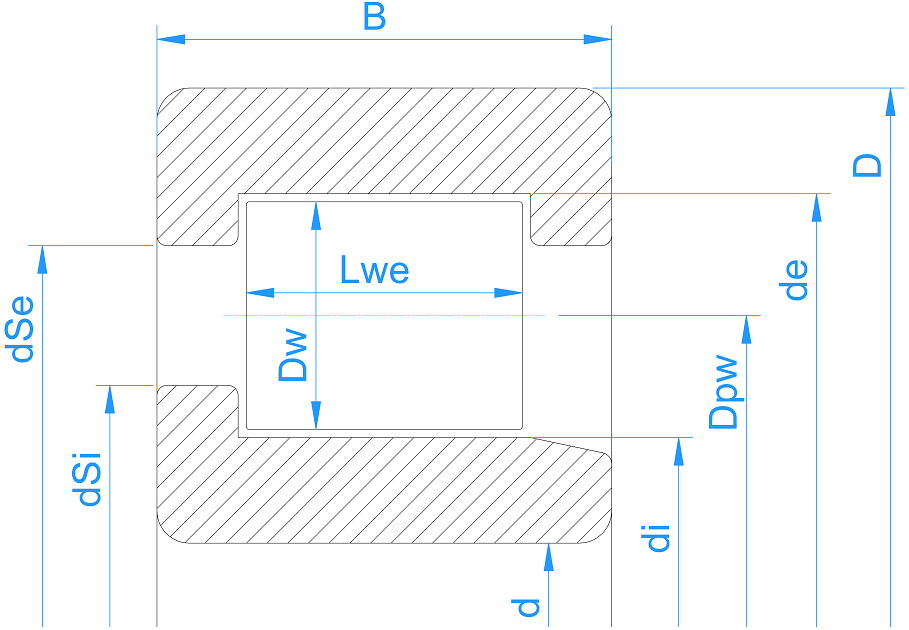
Cylindrical roller bearing (double row)
Double row cylindrical roller bearings are indicated to operate under similar circumstances to those applicable to the full complement single row bearings. The main difference is that they are in addition able to accommodate moment loads. Nevertheless they need to take up more axial space and are unsuitable to compensate any misalignment.
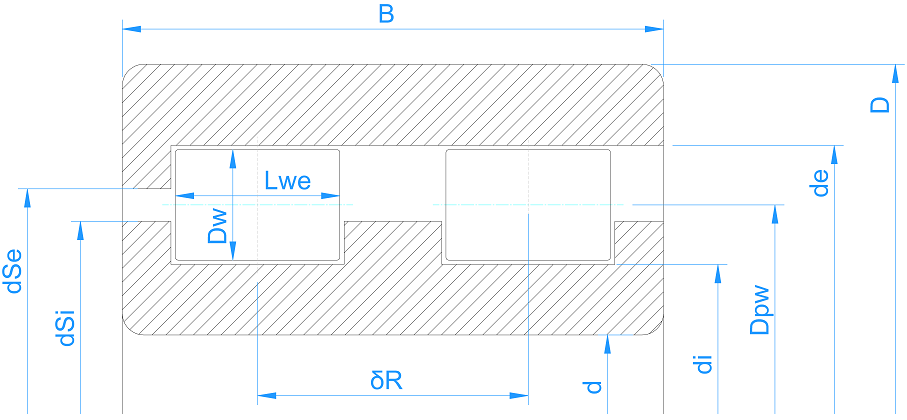
Spherical roller bearing
Spherical roller bearings have two rows of rollers wrapped under a common sphered outer ring raceway. Each row of rollers runs separately over a raceway on the inner ring inclined at an angle to the bearing axis. As the center point of the sphere in the outer ring raceway is at the bearing axis, the bearings are self-aligning and remain unaffected under any shaft misalignment relative to the housing; which obviously prevent them from being used for supporting moment loads. In fact, spherical roller bearings are conceived to accommodate heavy radial loads, as well as heavy axial loads in both directions, but in contrast they do not provide good performance if a high stiffness or low friction are required.
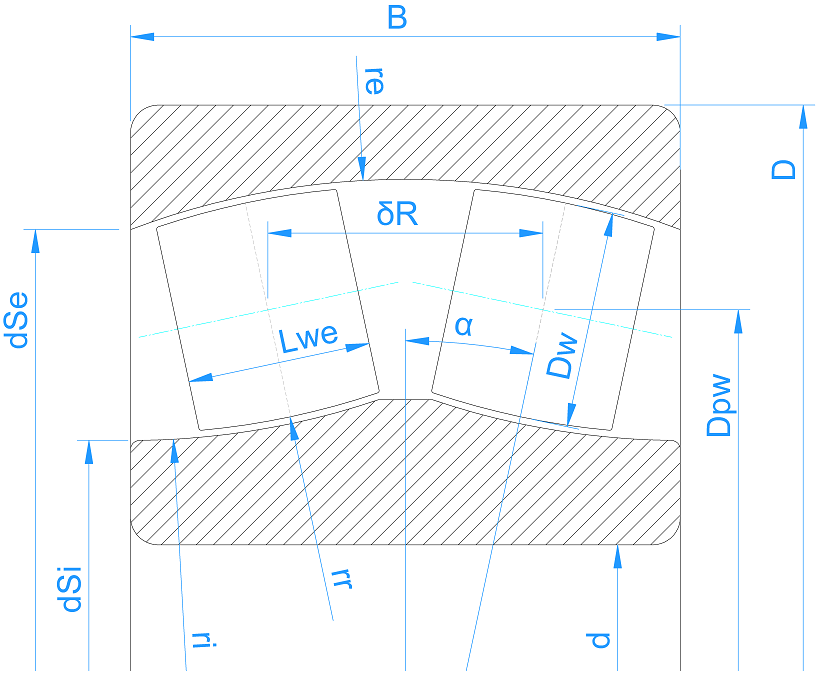
Barrel roller bearing
Barrel roller bearings are single row, non-separable, self-aligning roller bearings, that have either a cylindrical or tapered bore. They consist of solid outer rings with a concave raceway and inner rings which have two shoulders used to contain these particular bulb-shaped rollers. Barrel roller bearings are specially suitable where high radial shock type loads occur and misalignments need to be compensated. They take up less space than spherical roller bearing, but their axial load carrying capacity is in contrast quite poor since the effective contact angle is very small.
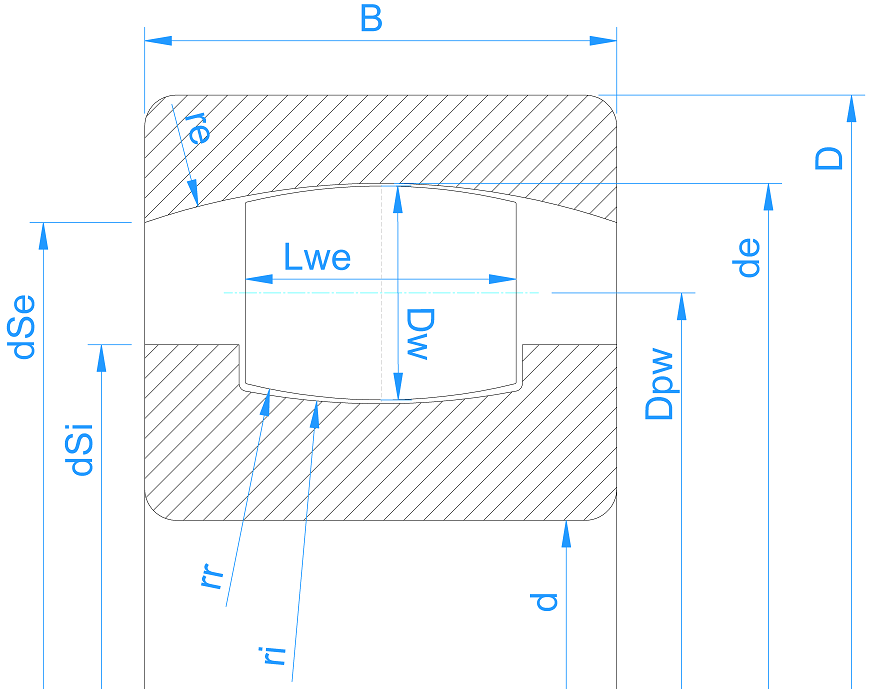
Tapered roller bearing
The tapered roller bearings consist of tapered rollers that run over tapered inner and outer ring raceways which are mostly either crowned or designed with a logarithmic profile to prevent stress peaks at the roller ends. They are conceived to support combined loads at medium relative speeds. In order to provide proper rolling, the projection lines of the raceways meet at a common point on the bearing axis, which serves to lower the friction. The bigger the contact angle is, the higher axial load carrying capacity of tapered roller bearings can be reached. Moments loads can be accommodated, but very poorly.
Very often their range of application areas can be extended by mounting sets of matched bearings. The matched bearings can be arranged in face-to-face, back-to-back or tandem. They deliver a higher capacity to withstand moments loads and heavy pure radial loads as well as axial loads in either direction at a time. As a counterpart, this arrangements are unsuitable to compensate any errors of initial alignment.
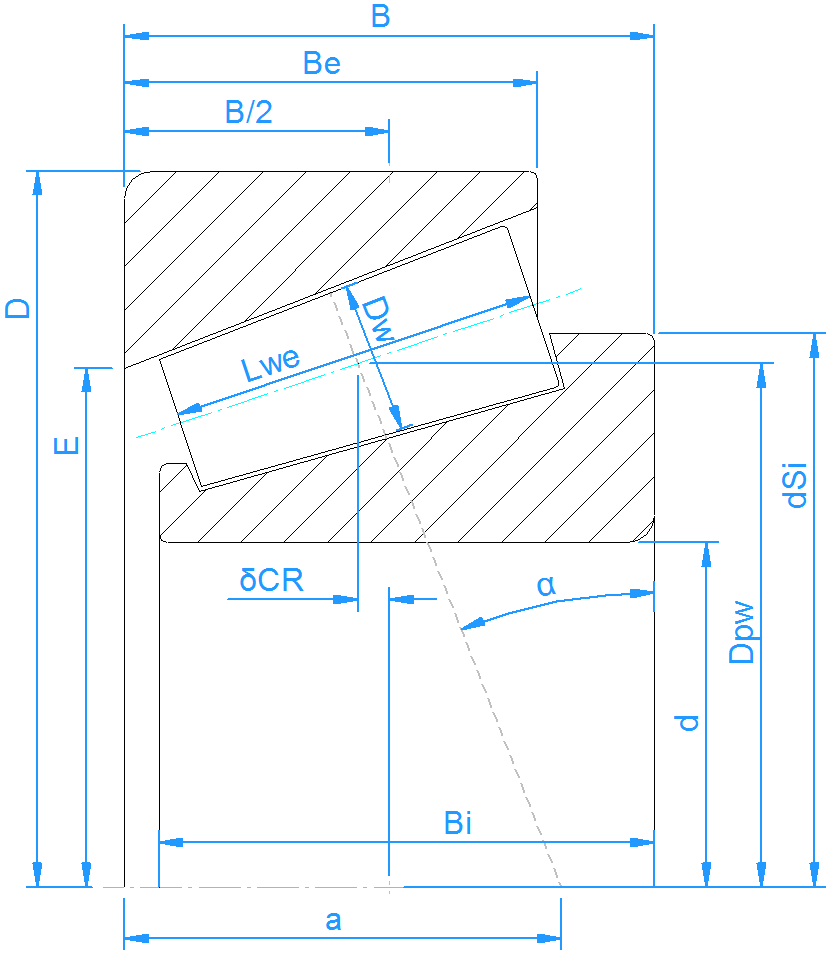
Needle bearing
For bearing arrangements where radial space is very limited, Needle roller bearings are to be considered. They are like bearings with cylindrical rollers whose diameter is small relative to their length and may even dispense with inner ring. Despite their reduced cross section, needle roller bearings have a high load carrying capacity and the ends of the rollers are slightly relieved to modify the line contact between the rollers and raceways. This avoids unwanted stress peaks at the roller ends, thus extending bearing service life. There are different designs that suit a wide range of operating conditions and applications. Generally, they are expected to have a higher friction and noise than in the case of cylindrical roller bearings.
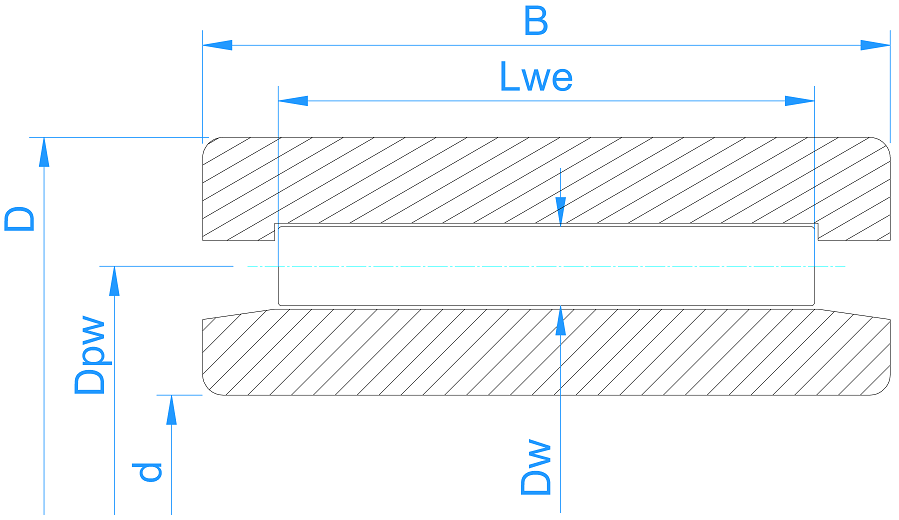
Crossed roller bearing
Crossed roller bearings are designed for precision applications as they are capable of supporting bearing loads in every direction with high rotation accuracy while conserving space and volume. The outer ring is split and is held together by three retaining rings. Since the cylindrical rollers are orthogonally arranged with respect to each other, these bearings can accommodate axial forces from both directions as well as radial forces, tilting moment loads and any combination of loads with a single bearing position. This feature allows other designs that require two bearing positions to be reduced to a single bearing position. Generally, crossed roller bearings bearings are very stiff and are supplied with normal clearance, little clearance or preload. They are optimal for the table bearing of machine tools, including vertical boring and grinding machines, and widely used in automatic control, robotics, medical and inspection devices.
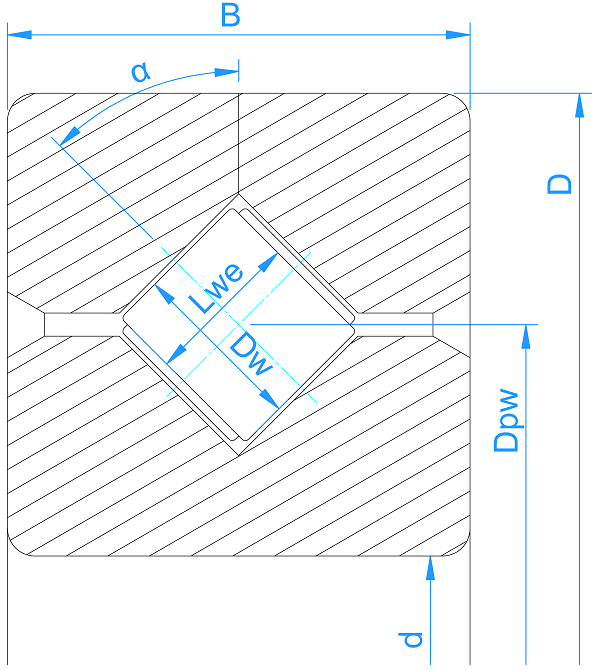